Digital transformation in manufacturing in 2023
Digital transformation is rapidly changing the entire manufacturing industry. Suffering from revenue, unproductive employees, outdated equipment, outdated software, outdated processes if his CIO in manufacturing does not understand what is best for current and future business and customers will be.
Every manufacturing process and organization is different and individual, so there are also examples of what and how can be implemented. To help CIOs, CTOs, and other manufacturing leaders start their digital transformation efforts, here are his eight examples of digitizing manufacturing.
Digital transformation in manufacturing 8 Examples
1. Industrial IoT Sensors
These devices measure and monitor industrial processes. It can be deployed on-site, in a manufacturing plant, or anywhere else you need to collect data on the performance of various devices. These include gas sensors that measure the amount of oxygen in a specific area, temperature sensors that monitor the temperature of objects or processes, and pressure sensors that measure changes in air pressure around the device.
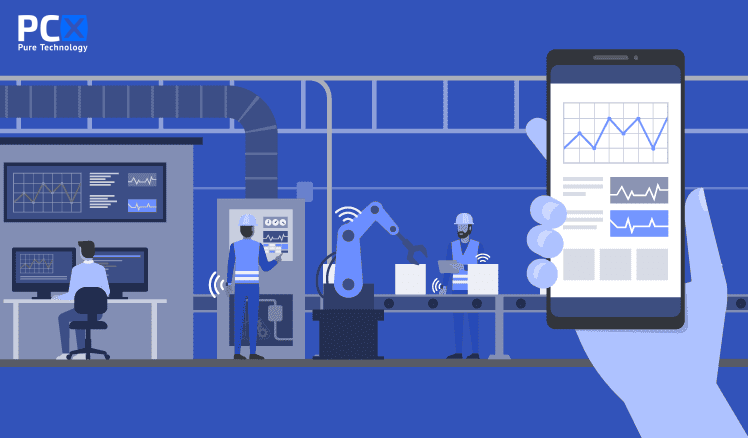
Some of the most common applications for industrial Internet of Things (IoT) sensors include:
- Plant and Equipment Operation Monitoring
- Energy Consumption Monitoring
- Inventory Management
- Device Maintenance Tracking
- Measuring Environmental Conditions such as Humidity and Temperature
2. Big Data and Analytics
Big data refers to the increasing volume, velocity, and variety of data that companies generate and collect. Its ability to measure performance and improve overall efficiency has made it a critical part of business operations.
Big Data enables manufacturers to identify and respond to business trends. Make informed decisions about product development, supply chain management, and other important aspects of running a manufacturing company.
3. AI, Automation & Machine Learning
AI-powered digital transformation is transforming manufacturing companies into smarter, leaner and safer businesses. One of the most exciting things about artificial intelligence (AI), automation, and machine learning is that it can make manufacturing companies more efficient by automating a variety of tedious processes for workers. It also enables manufacturers to predict trends more accurately, improve quality control, produce products faster and reduce waste.
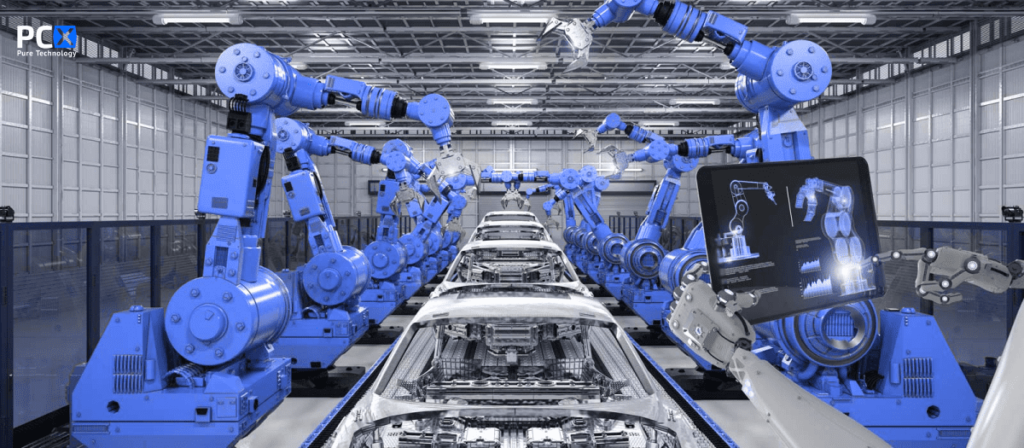
Manufacturers are already using these technologies in many ways. For example, businesses can use AI technology to analyze data from customer orders to ensure they get what they want when they order something. Another company may use machine learning to find patterns in customer data and predict what products they are likely to purchase next.
4. Cloud-Based ERP and Other Manufacturing Software
Cloud-based enterprise resource planning (ERP) systems and other manufacturing software are applications that provide tools for managing business processes. A cloud-based ERP system allows your company’s data to be stored in the cloud so you can access it from anywhere. Implementing her new ERP makes it easier for employees to collaborate on projects and access information, even when away from their desks. You can also use cloud-based ERP software to manage inventory, production, customer relationships, and more.
Manufacturers are increasingly turning to cloud-based ERP systems to streamline operations. These systems give manufacturers access to the same tools they use in the office, allowing them to spend less time on paperwork and more time on what they do best: product development.
5. Smart Manufacturing
Smart Manufacturing is a term used to describe the use of digital technology and automation to communicate with other devices or systems and collect data about the system’s behavior.
Intelligent manufacturing can be applied to all aspects of manufacturing, including production control, quality control and supply chain management.
The goal of smart manufacturing is to use new technologies to make processes more efficient and productive.
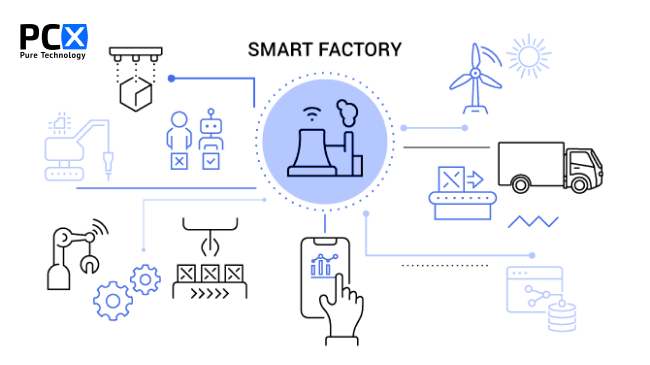
The main advantages of intelligent manufacturing are:
- Improved quality control and production planning
- Improved inventory planning
- Faster problem resolution
- Lower overall costs
6. 3D Printing
3D printing is one of the most innovative manufacturing technologies in recent years and is already being used in other industries to develop new products.
3D printing is the process of creating objects from digital data. A laser is used to apply a layer of material and harden it to create an object. This technology can be used to create whole objects or the parts that make them up.
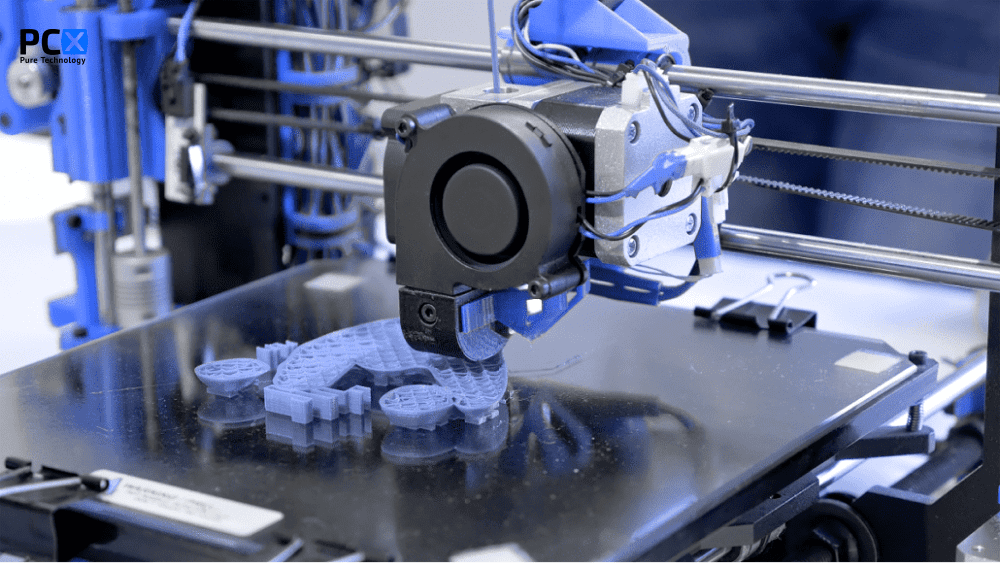
7. Predictive Maintenance
Predictive Maintenance is a methodology that helps manufacturers monitor equipment and machinery for signs of wear. It also helps predict when parts will need to be replaced or repairs needed before they break.
In this way, it is similar to preventive maintenance, which prevents problems in the first place. However, predictive maintenance also provides insights that can help reduce downtime and improve operational efficiency.
Predictive maintenance systems are used in a variety of industries, including automotive, oil and gas, building construction and maintenance, and pharmaceuticals.
A predictive maintenance system constantly monitors the condition of equipment and makes adjustments as necessary. This means that even if you’re not looking at your gear, it’s already working to keep your gear in tip-top shape.
This type of system also has the advantage of preventing problems before they occur, saving repair and maintenance costs.
8. Augmented Reality and Virtual Reality
Augmented Reality and Virtual Reality are two terms that are often used interchangeably, but they are quite different.
Augmented reality is the augmentation of the user’s environment with computer-generated information. This can be seen in the diagram below.
Virtual reality is the complete immersion of the user in a digital environment.
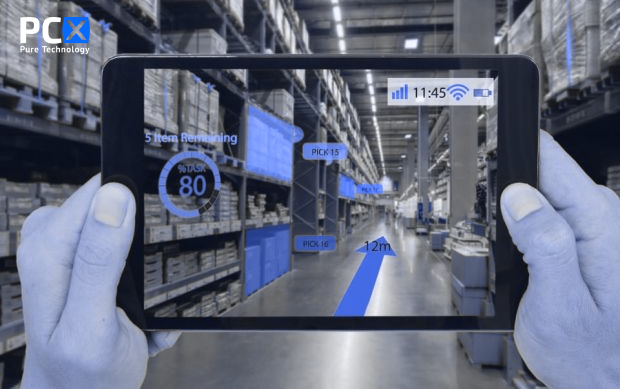
Leave a Reply